
Hot Air Gypsum Board Production Line
Fully automatic gypsum board production line is a special equipment for producing flat-packed gypsum board for new building materials.
Fully automatic gypsum board production line is a special equipment for producing flat-packed gypsum board for new building materials.The production line consists of the following parts:batching system,molding system,solidification system,automatic cutting system,transfer system,distributor system,drying system,packaging system.
Processing chart
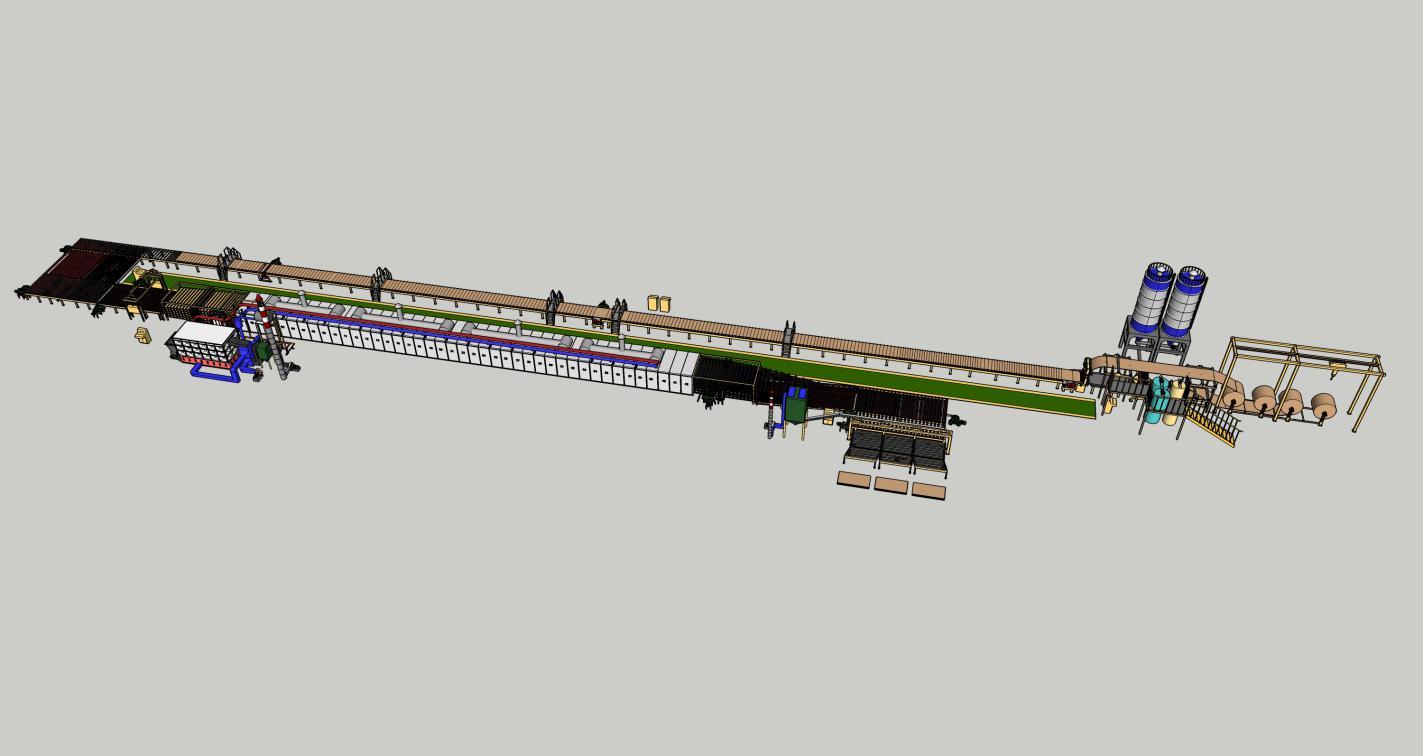
Detail parameters of gypsum board production line
Production capacity:2million~30 million square meter per year.
Final product variety:
(1)Common paper-faced plasterboard
(2)Fire resistance paper-covered plasterboard,
(3)Water resistance paper-covered plasterboard.
Product specification:
Board length:2000--3600mm
Board width:1200mm、1220mm
Board width:1200mm、1220mm
Board thickness:8--25mm
General gypsum plaster board length 2400mm,width 1200mm,thickness 9.5mm.
Main equipment introduction
Dosing System
Accurate dosing for each raw material. Starch mixing tank use stainless steel, with long service life and low corrosive.The foaming agent reserve tank is made of stainless steel. Foaming system adopts domestic advanced technology-Dynamic and static foaming system, ensuring the finished board is lightweight, good toughness and saving much cost.
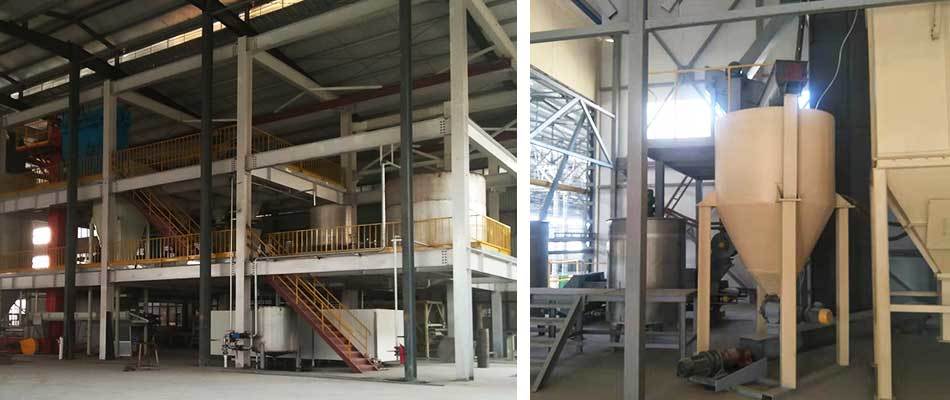
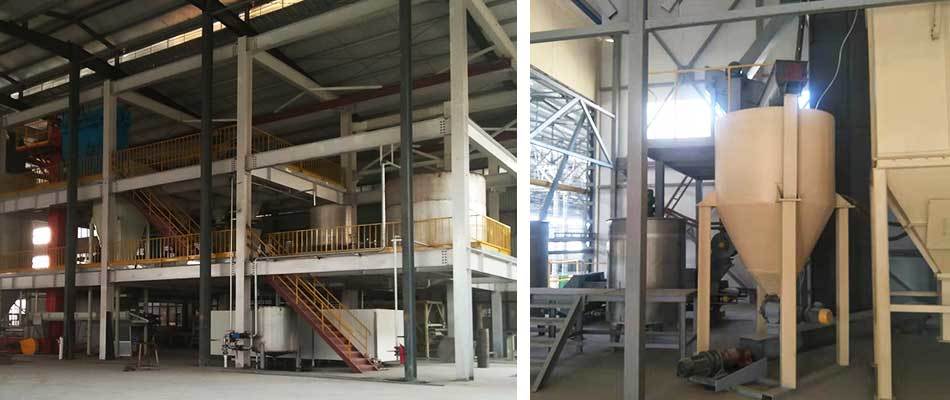
Forming System
gypsum slurry from the vertical mixer falls onto the forming line lower paper, the upper paper by the correcting device, glue device sent to the forming station, through the vibration table, the lower paper folding cover upper paper and squeezes out plasterboard of requested specification.
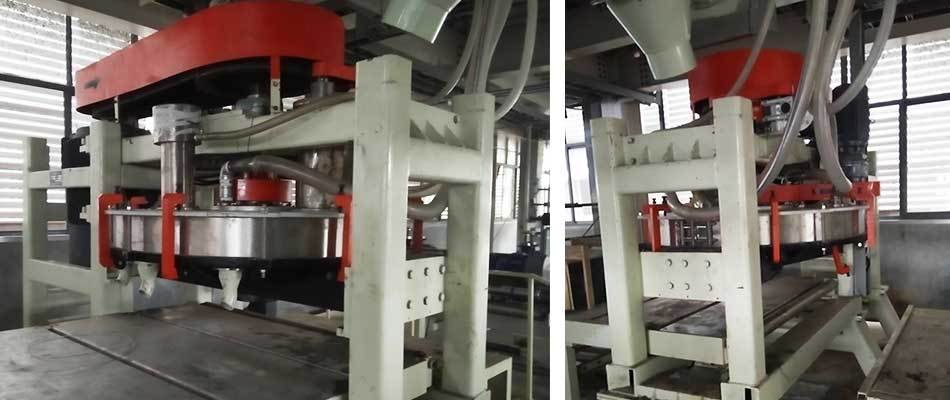
Solidification System
Finished the initial solidification on belt, and final solidification on Conveying roller.
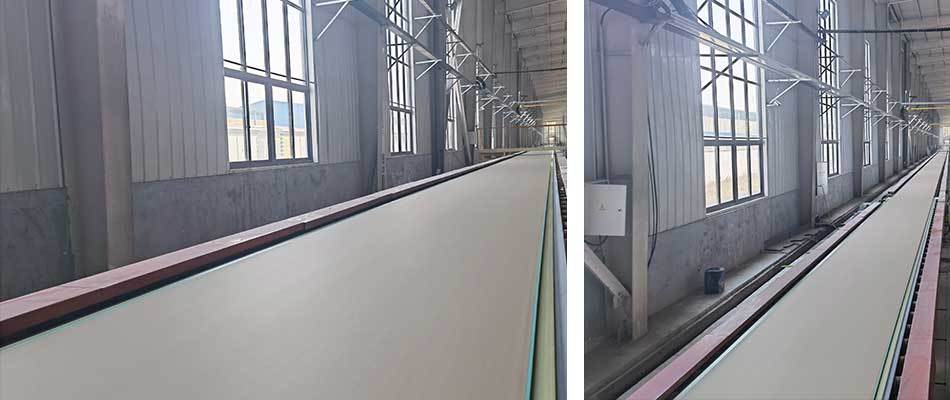
Automatic Cutting System
With the adoption of developed core servo cutting technology of our company, adjusting the required plate dimension by digital controller. only1 mm gap between cutting saw,Maximally reducing cost by controlling the minimum edge horn size.
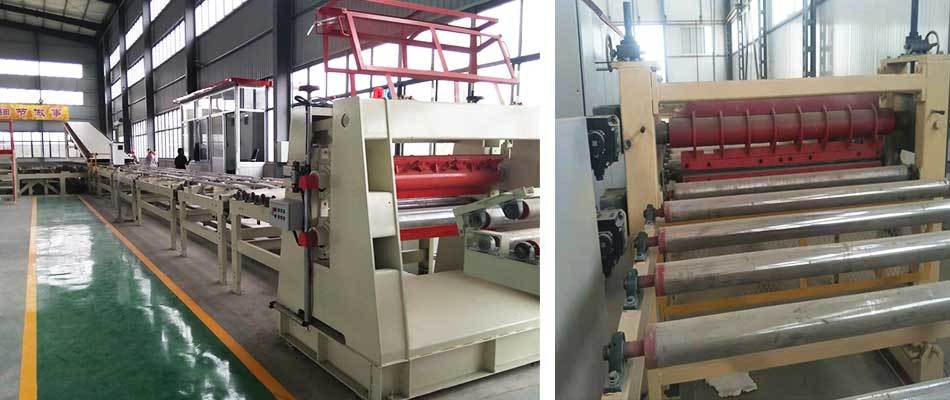
Transit System
Used to horizontally transport the cut plate to distributor,The adopting of servo motor control ensures the precision of the board movement position.
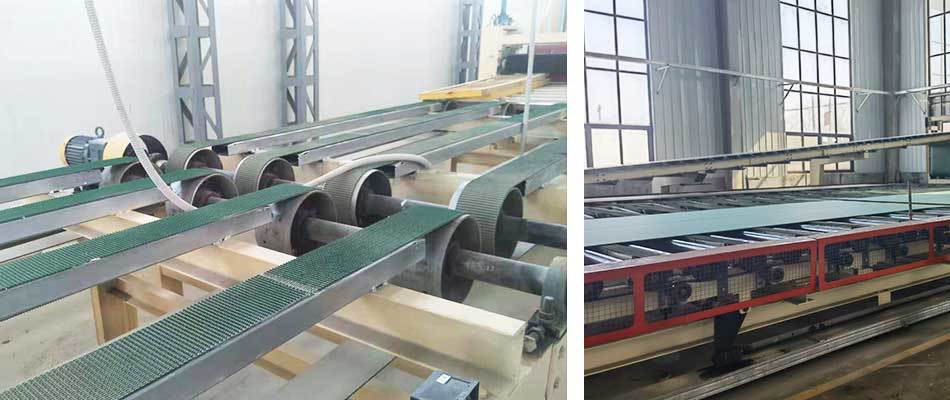
Drying System
The board enter into the drying room through distributor, Drying room is divided into 2 areas: heating area and cooling board area, After drying machine finished drying task, out board machine discharging board.
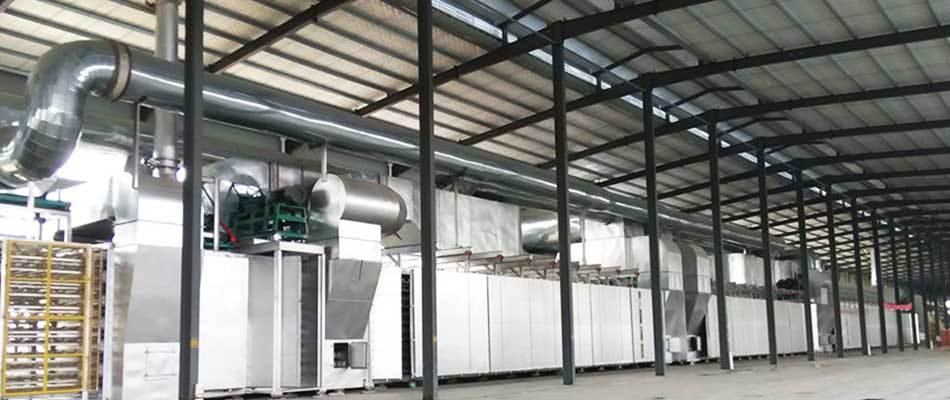
Discharging Board And Finished Board System
Used to convey gypsum board,and cutting to get required size, then edging and stacking.
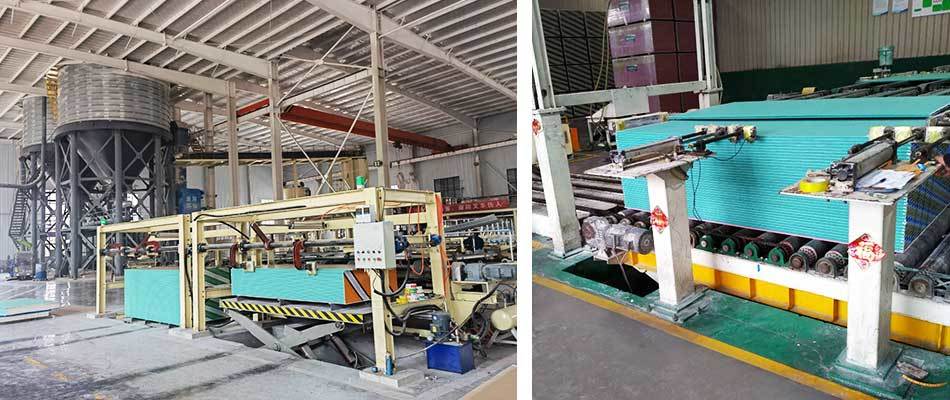
Finished Board
1. Newly developed technology,curved edge gypsum boards
2. New developped foamed gypsum board is more lightweight , so easy for installation ,also strenght is higher
Technology Advantage
1. The heat supply of the entire production line uses only one heat exchange, which reduces the heat loss during multiple heat transfer. It is heated by the flue gas of the hot blast stove through the heat exchanger to the temperature required for production, and then the clean gypsum board is dried by clean hot air. In the process of drying, the hot air can be fully contacted with all sides of the gypsum board for drying, so that the problem of dryness of the gypsum board can be better ensured by the problem of low heat on one side and low heat on one side.
2. The whole process of drying is designed by using the hot air circulation method. The fully enclosed system is used in the dryer to ensure that the heat loss during the heat transfer process is minimized, thereby reducing the energy consumption requirement. During the drying process, the entire drying chamber is divided into several zones. We adjust the temperature and flow of the hot air according to the temperature required by each zone, which can save energy.
3. The heating time is short. Only when the hot blast stove is completely burned can the temperature required for the production process be quickly reached.
4. The equipment is easy to operate and easy to control.
5. At present, more than 20 million gypsum board production lines in China use hot air dryers to dry gypsum boards.
2. The whole process of drying is designed by using the hot air circulation method. The fully enclosed system is used in the dryer to ensure that the heat loss during the heat transfer process is minimized, thereby reducing the energy consumption requirement. During the drying process, the entire drying chamber is divided into several zones. We adjust the temperature and flow of the hot air according to the temperature required by each zone, which can save energy.
3. The heating time is short. Only when the hot blast stove is completely burned can the temperature required for the production process be quickly reached.
4. The equipment is easy to operate and easy to control.
5. At present, more than 20 million gypsum board production lines in China use hot air dryers to dry gypsum boards.
production
the
system
board
of
and
is
drying
cutting
gypsum
PROVIDE SOLUTIONS FOR YOUR INDUSTRY